Oil seal as a mechanical seal element, its material performance is directly related to the sealing effect and service life. Different rubber materials have their own unique performance characteristics and are suitable for different working environments and media. The following are some common rubber materials and their application characteristics in oil seals:
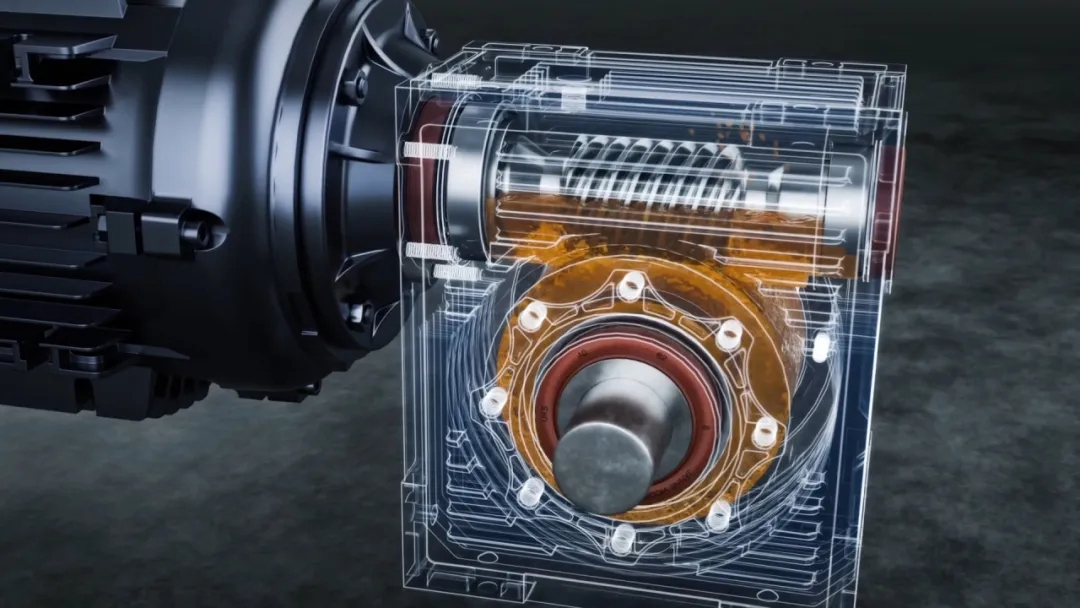
No.1 Nitrile rubber (NBR)
Nitrile rubber is one of the most commonly used rubber materials in the making of oil seals, mainly thanks to its good oil resistance and low price. It is made from two monomers, butadiene and acrylonitrile, by emulsion or solution polymerisation, and is a kind of polar, unsaturated, non-crystalline rubber. NBR has good oil resistance, abrasion resistance, heat resistance and adhesive strength, and is suitable for long-term use in air at 120°C or in oil at 150°C. It has a low temperature resistance and a low price. However, it is less resistant to low temperatures and ozone, has inferior insulating properties and slightly lower elasticity, so it may not achieve the desired sealing effect under extreme conditions.
No.2 Fluoroelastomer(FKM)
Fluoroelastomer has excellent resistance to high temperatures, oxidation, oil, corrosion and atmospheric aging, as well as a high degree of chemical stability. It is one of the best media resistance among all elastomers. Viton oil seals can work for a long time at 200°C-250°C. They are suitable for extreme conditions such as engine seals, chemical industry seals, deep well oil extraction equipment and superheated steam seals. However, Viton is more costly and may not be as durable as other materials under certain conditions.
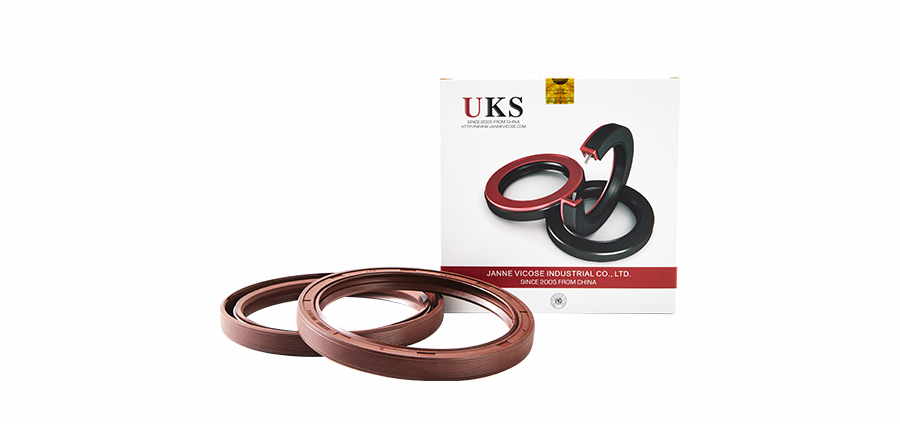
No.3 Hydrogenated NBR(HNBR)
Hydrogenated NBR saturates the hydrocarbon chain of NBR through a hydrogenation reaction, resulting in improved resistance to heat, oil, ozone and abrasion. It performs well in very high temperature environments and fills the gap between NBR and Viton in some areas of application. However, hydrogenated NBR is not resistant to polar solvents and has reduced elasticity at low temperatures.
No.4 Acrylate rubber(ACM)
Acrylate rubber has excellent heat and oil resistance, the use of temperature can be as high as 180 ℃ -200 ℃, widely used in products requiring high temperature and heat oil resistance. It also has good resistance to ozone, flexing, sunlight aging, air tightness and other characteristics, suitable for high temperature seals in the automotive industry.
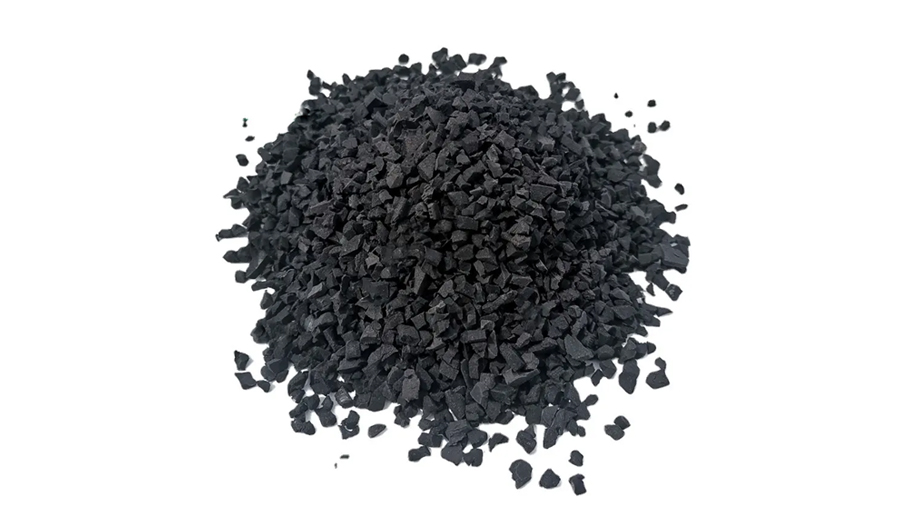
In summary, choosing the right rubber material is crucial to ensure the performance and life of the oil seal. Different working environments and media require the selection of different rubber materials to achieve the best sealing effect and service life.
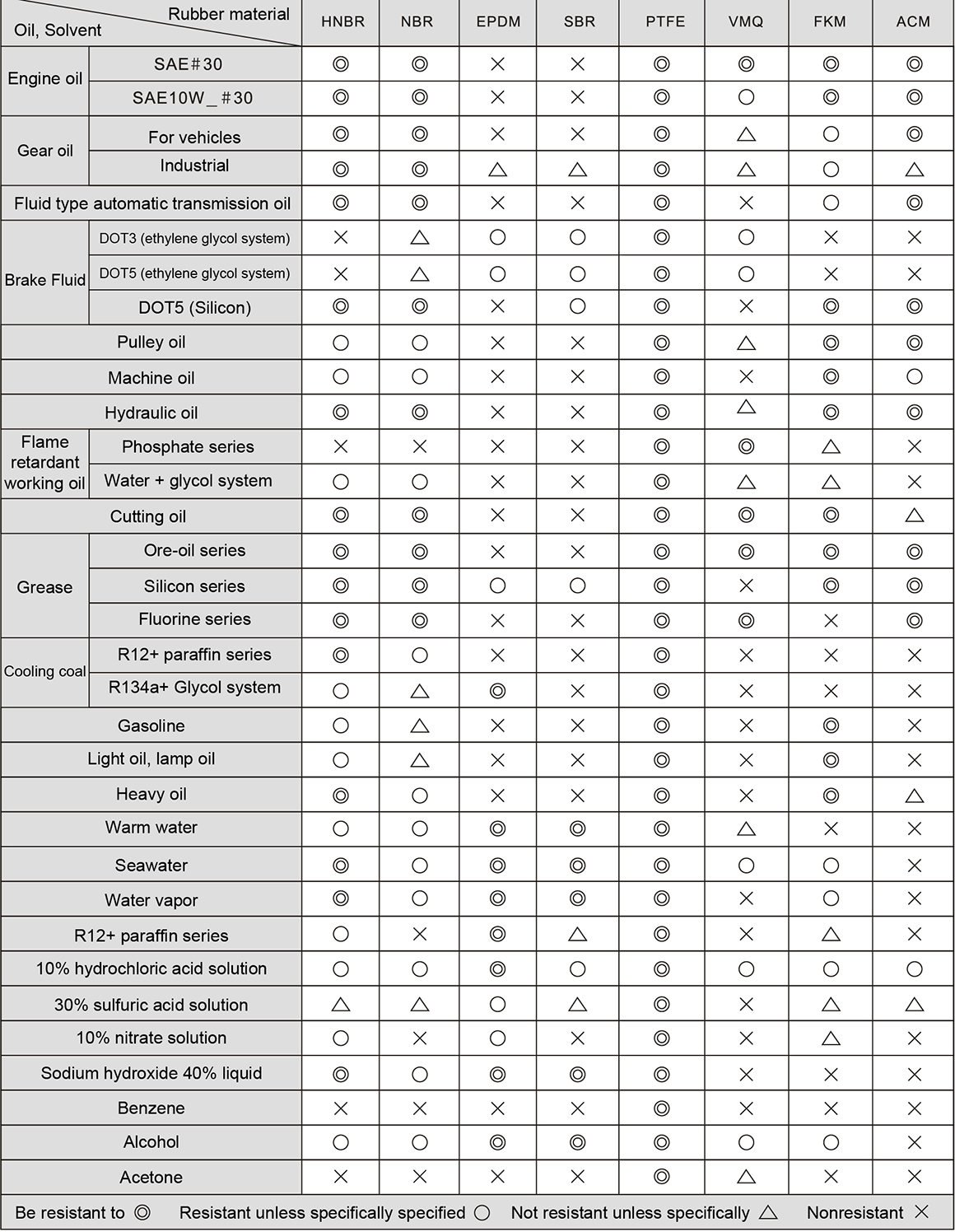
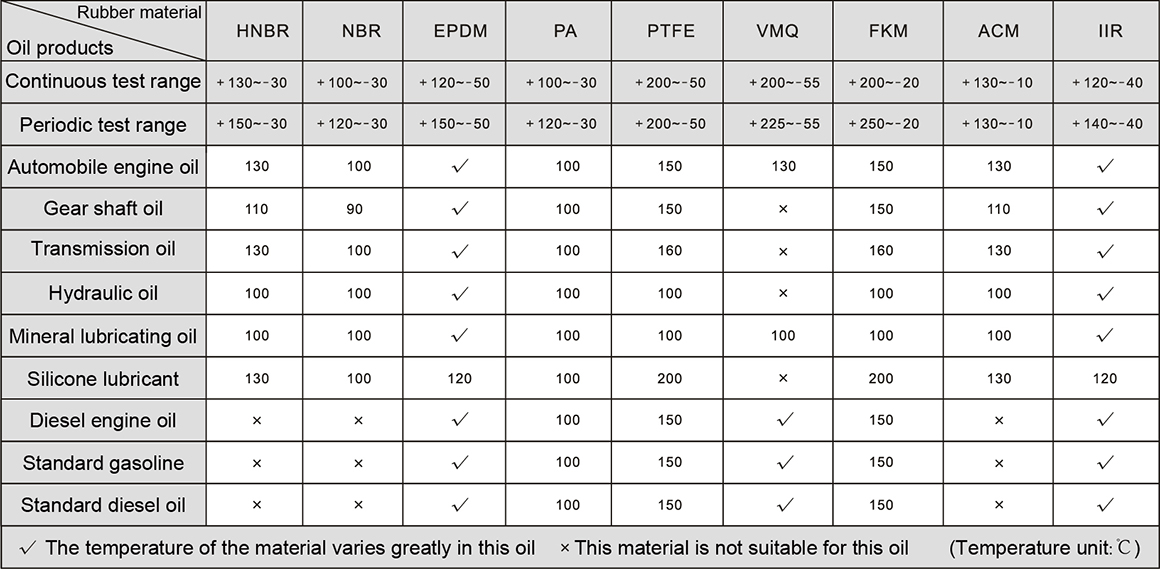
The quality difference between the same type of rubber, there is also a huge difference. Good rubber raw materials matched with scientific formulas, coupled with a rigorous vulcanisation system, can only produce stable seals. uks never hesitates to use materials, and never selects only international high quality rubber materials. We believe that only good materials are the basis for excellent quality.